Laminacja płomieniowa (termiczna) – na czym polega i zalety rozwiązania
Laminacja płomieniowa to proces technologiczny, który znalazł szerokie zastosowanie w wielu branżach, takich jak motoryzacja, tapicerstwo czy produkcja sprzętu rehabilitacyjnego i wielu innych. Technika ta polega na wykorzystaniu otwartego płomienia do nadtopienia powierzchni pianki, co pozwala na trwałe połączenie co najmniej dwóch materiałów warstwą pianki poliuretanowej, bez potrzeby stosowania dodatkowych klejów. Ta metoda łączenia jest ceniona za swoją efektywność, trwałość i szerokie zastosowanie, a połączone materiały zyskują dodatkową funkcjonalność i unikalne cechy.
Na czym polega laminowanie materiałów?
Laminacja płomieniowa, znana również jako laminacja termiczna, to technika stosowana do łączenia materiałów różnego rodzaju, takich jak tkaniny, dzianiny, folie, gumy czy tworzywa sztuczne. Wśród laminatów płomieniowych wyróżniamy dwu-sklejki, które wykonane są z materiału wierzchniego oraz pianki oraz trój-sklejki, wykonywane z dwóch materiałów oraz pianki pomiędzy nimi. Proces ten polega na wykorzystaniu otwartego płomienia do stopienia warstwy elastycznych pianek (najczęściej poliuretanowych), które są pomiędzy materiałami, co umożliwia ich trwałe połączenie bez konieczności stosowania dodatkowych technologii klejenia.
Ta metoda jest ceniona za swoją efektywność, szybkość realizacji oraz zdolność do tworzenia mocnych i trwałych połączeń, a także za redukcję kosztów, ponieważ eliminuje potrzebę stosowania zewnętrznych adhezyjnych substancji na poszczególne warstwy materiałów. Jednakże wymaga precyzyjnej kontroli warunków procesu, aby uniknąć uszkodzenia wrażliwych tworzyw i zapewnić równomierne i efektywne połączenie pianką poliuretanową.
Jak przebiega laminacja płomieniowa?
Laminacja płomieniowa jest skomplikowanym i złożonym procesem, który wymaga precyzyjnego przygotowania oraz wykonania w celu osiągnięcia oczekiwanych wyników. Każdy etap procesu ma kluczowe znaczenie dla jakości i trwałości finalnego produktu.
- Przygotowanie materiałów - pierwszym i fundamentalnym krokiem w procesie laminacji płomieniowej jest staranne przygotowanie materiałów.Obecnie dostęp do najróżniejszych typów materiałów jest niemalże nieograniczony. Technologia produkcji tekstyliów i materiałów technicznych oferuje szeroki wachlarz podstawowych oraz bardziej zaawansowanych rozwiązań. W przypadku dalszego przetwarzania materiału, warto zadbać o pozyskanie produktu od sprawdzonego dostawcy, który stosuje standardy jakościowe. Materiały pozyskane ze sprawdzonych źródeł często nie wymagają przygotowania przed laminacją co skraca czas realizacji oraz obniża jej koszt. Warstwy, które mają być ze sobą połączone, przede wszystkim powinny być równo nawinięte na kartonowej tulei, wolne od zagnieceń oraz zanieczyszczeń. W przypadku gdy materiał jest dostępny w nawojach o małym metrażu, przygotowanie do produkcji polega na połączeniu mniejszych odcinków w jedną większą belkę aby zwiększyć wydajność procesu laminacji.
- Przewleczenie materiałów - przed przystąpieniem do laminowania, materiały wprowadzane są do maszyny przez operatora. Maszyna do laminacji płomieniowej to ciąg technologiczny składający się z wielu modułów z różnymi systemami wałków, po których porusza się materiał. Na tym etapie kluczowe jest przeprowadzenie wstęgi poszczególnych materiałów przez odpowiednie wałki. Z uwagi na właściwości różnych typów materiałów, stosuje się kilka układów przeleczeń. Odpowiednie poprowadzenie materiału przez maszynę pozwala uniknąć wielu potencjalnych błędów.
- Laminacja (łączenie) - Wstęga pianki poliuretanowej jest nadtapiana płomieniem w module nazywanym głowicą. Głowice o odpowiedniej konstrukcji, w których zamontowano dwa zestawy palników, umożliwiają nadtopienie pianki z obu stron podczas jednego przebiegu procesu. Bezpośrednio za palnikami znajdują się wałki dociskowe, w których nadtopiona pianka zbiega się z laminowanym materiałem. Bardzo ważnym elementem procesu laminacji płomieniowej jest dostosowanie trzech kluczowych parametrów pracy maszyny, którymi są prędkość, intensywność płomienia oraz docisk.
- Nawijanie laminatu - materiały po przejściu przez moduł główny tworzą trwale połączone warstwy, które od tej pory można nazywać laminatem. Kolejne moduły maszyny służą do wykonywania operacji dodatkowych, takich jak wyrównywanie brzegów lub nadruk oznaczeń identyfikacyjnych. Ostatnim modułem maszyny do laminacji płomieniowej jest nawijak. Laminat nawija się na rolni o dużym metrażu, na wózkach transportowych. W przypadku niektórych typów pianek, laminat jest sezonowany aby wytopiony z pianki klej odpowiednio złączył się z pozostałymi warstwami. Jednak najczęściej laminat jest gotowy do przewijania od razu po zakończeniu laminacji.
- Przewijanie - ostatnim etapem procesu laminacji płomieniowej jest przewijanie laminatu z wózków transportowych na docelowe belki z kartonową tuleją w środku. Rozmiar belek zależy od specyficznych wymagań klienta oraz determinuje dalsze transportowanie i magazynowanie wyrobu. W trakcie przewijania przeprowadzana jest również kontrola jakości polegająca na badaniu parametrów laminatu oraz ocenie wizualnej.
Laminowanie płomieniowe - zalety
Zalety laminacji płomieniowej sprawiają, że metoda ta jest powszechnie stosowana w różnych sektorach przemysłu. Każdy z jej aspektów wnosi istotne korzyści, które przekładają się na efektywność produkcji i jakość końcowego produktu.
Silna i trwała spoina
Jedną z głównych zalet laminacji płomieniowej jest tworzenie silnej i trwałej spoiny. Proces ten zapewnia dodatkową funkcjonalność oraz pozwala na połączenie materiałów w sposób, który jest odporny na rozrywanie, rozwarstwianie oraz inne uszkodzenia mechaniczne. Dzięki temu produkty wytworzone tą metodą charakteryzują się wyższą wytrzymałością, co jest kluczowe w przypadku elementów narażonych na ciężkie warunki eksploatacyjne. Mocne połączenie zapewnia także lepszą szczelność i odporność na wpływ warunków atmosferycznych, co jest nieocenione np. w produkcji tapicerki samochodowej, czy sprzętu rehabilitacyjnego.
Wszechstronność zastosowań
Kolejną znaczącą zaletą laminacji płomieniowej jest jej wszechstronność. Technika ta może być stosowana do różnorodnych materiałów, takich jak materiały z włókien naturalnych, tworzywa sztuczne, folie, czy gumy, co pozwala na jej zastosowanie w wielu gałęziach przemysłu, od produkcji motoryzacyjnej, przez tekstylia, aż po opakowania i produkty konsumenckie.
Szybkość i wydajność procesu
Laminacja płomieniowa wyróżnia się również szybkością i wydajnością procesu. Dzięki możliwości szybkiego łączenia dużych powierzchni w krótkim czasie metoda ta pozwala na znaczące zwiększenie tempa produkcji. Szybki czas przetwarzania i brak potrzeby długotrwałego schnięcia kleju, jak ma to miejsce w innych technikach laminowania, czynią laminację płomieniową idealnym rozwiązaniem dla projektów wymagających szybkiej realizacji.
Koszty produkcji
Ostatnim, lecz nie mniej ważnym, aspektem jest koszt. Laminacja płomieniowa jest stosunkowo niedrogą metodą łączenia, szczególnie w porównaniu do bardziej zaawansowanych metod, takich jak laminacja klejowa. Niskie koszty, brak potrzeby stosowania drogich materiałów eksploatacyjnych (takich jak kleje specjalistyczne), oraz redukcja czasu pracy przyczyniają się do obniżenia ogólnego kosztu produkcji, co jest atrakcyjne z punktu widzenia producentów szukających efektywnych i ekonomicznych rozwiązań.
Laminacja płomieniowa to wszechstronna i wydajna metoda łączenia różnych materiałów, która cieszy się popularnością w wielu sektorach przemysłu. Jednym z głównych atutów tej technologii jest tworzenie silnej i trwałej spoiny, która jest odporna na działanie wielu czynników zewnętrznych. Dodatkowo laminacja płomieniowa przyciąga uwagę dzięki swojej szybkości realizacji procesów oraz niskim kosztom operacyjnym, co czyni ją atrakcyjną ekonomiczną opcją w porównaniu do innych metod łączenia materiałów.
Jeśli szukasz specjalisty w tworzeniu laminatów techniczno-tekstylnych dla wymagających branż to dobrze trafiłeś! Zachęcamy do kontaktu w celu omówienia szczegółów współpracy.
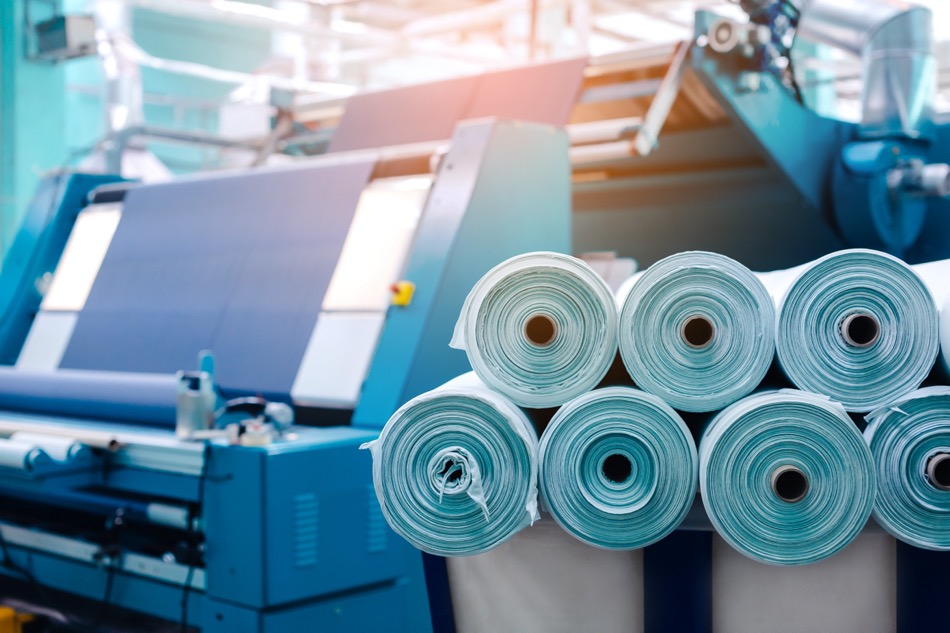

Firma MAGNETIX LAMINATION Sp. z o.o. Sp. k. uzyskała dotację z Unii Europejskiej na projekt „Wdrożenie strategii wejścia przedsiębiorstwa na nowe rynki zagraniczne, jako droga do zwiększenia skali potencjału eksportowego przedsiębiorstwa MAGNETIX”.
Celem głównym projektu jest wzrost konkurencyjności firmy MAGNETIX na rynku międzynarodowym, poprzez budowę świadomości marki produktowej wśród odbiorców zagranicznych. Cel zostanie osiągnięty poprzez rozwinięcie eksportu, pozyskanie nowych, kluczowych klientów oraz dywersyfikację sprzedaży na nowych rynkach, promocję i budowę konkurencyjnej pozycji Marki na rynku zagranicznym.
Przedmiotem projektu będzie zdobycie nowych rynków zagranicznych, jakimi są rynki austriacki i holenderski.
Zgodnie ze sporządzonym Modelu Biznesowym, w ramach projektu zostaną zrealizowane rekomendowane działania:
– udział w największych europejskich specjalistycznych targach branżowych, jako wystawca;
– udział w imprezach targowych jako odwiedzający;
– zakup usług doradczych związanych z wyszukiwaniem i doborem partnerów na rynkach docelowych;
– przygotowanie i produkcję indywidualnych materiałów promujących produkty na nowych rynkach zbytu.
Z projektu korzystać będą pracownicy, którzy w sposób bezpośredni lub pośredni będą zaangażowani w realizację powyższych zadań i osoby zarządzające przedsiębiorstwem. Projekt skierowany jest do potencjalnych klientów firmy z rynków zagranicznych, gdzie w ramach celu założono pozyskanie 10 kontraktów handlowych.
#FunduszeUE
Wartość projektu: 548 080,48 zł
Wysokość wkładu z Funduszy Europejskich: 378 754,79 zł